
Compound semiconductor substrate vendors continue to improve product quality and scaling. MBE equipment suppliers continue to offer innovations the need remains to develop next generation MBE with bettter stability and far lower particle counts, just to name a few. MBE-produced electronic and optoelectronic devices benefit from the interfacial abruptness, layer purity, and doping control and remain at the forefront of performance. MBE production has been shown effective for a range of current epi-wafer products, including pHEMTs, high-speed PINs and APDs, InP HBTs, lasers, and IR devices. The future is bright for MBE as a mass production tool for electronics and optoelectronics applications. Yung-Chung Kao, in Molecular Beam Epitaxy (Second Edition), 2018 32.12 Conclusion If this were greater than the dump-height of the backhoe, either a two-stage feeding arrangement or a larger back hoe would be needed. Locating a grizzly screen above the hopper to scavenge out the waste material might even out the flow to the plant but would certainly add to the required headroom. The usual loading arrangement is not suitable for a feed containing boulders and large trash because of the requirement of an additional screening facility ahead of the trommel. Generous degrees of over-design in the feed preparation section will usually pay handsome dividends in terms of increased gold recovery.Ī third problem is limited headroom due to restricted machine dump heights. This is significant operationally and the surge capacity must be large enough to iron out any fluctuations in the feed rate that might affect the smooth running of the recovery units. Digging rates in the bottom layers, including cleaning up at bedrock may be less than 50% of the rates achieved in the upper layers. The result will be loss of production time and/or loss of gold in unslurried material rejected from the plant.Ī second problem is posed by feed rate variations caused by digging at different levels between surface and bedrock. This cannot be guaranteed because the dumped load may contain some surprises in the form of boulders, timber, lumps of clay, fragments of bedrock, etc. Each bucket load then has only 30 seconds to be ingested smoothly into the system before the next load arrives. For example, if the back hoe has an average digging cycle of, say, 30 seconds, surges of material broken from the face will be dumped into the feed hopper at intervals of about 30 seconds. Provided that it is operated according to the manufacturer’s instructions the main problems are likely to be found in trying to match the intermittent flow of materials fed directly from the back hoe to the treatment plant. The back hoe is a useful production tool in small tributaries or narrow channel sections of large deposits that are being exploited by other means, e.g. Macdonald, in Handbook of Gold Exploration and Evaluation, 2007 Operational problems Die design, including the choice of die material, is only improved through practice on the production line with full-scale equipment.Įoin H. Also, studies to determine tool life have not yet been conducted mathematically or through modeling materials even scaled-down models are not very useful. On the other hand, complex deep-drawing studies cannot be made with plasticine, wax, or lead but can be conducted successfully on a scaled-down model using the real material. For the study of die design to prevent unfilled corners and cracks due to folding, modeling materials are most helpful. At present, however, experimental work is the only practical solution.

For example, the study of flow patterns for complex forging may one day be conducted analytically or by numerical procedures. However, when a specific problem arises, the pressure of time may dictate experimental methods. The potential for the application of analytical methods is unlimited. When an analytical solution is applied successfully to a new problem, the technique itself advances further, making the next solution for another problem easier and more reliable. The analytical criterion, on the other hand, is universal it applies anywhere and to any material. Every new appearance of the phenomenon called for a new study, but the resolution of the problem did not add to the understanding of the causes of the defect or to a solution to the problem when it appeared again. As a matter of fact, experimental procedures were employed successfully for the elimination of central burst, when discovered, prior to the development of the criteria. The specific problem that prompted the central-burst study could have been solved by a trial-and-error experimental procedure in a few weeks or months by personnel without an analytical background.
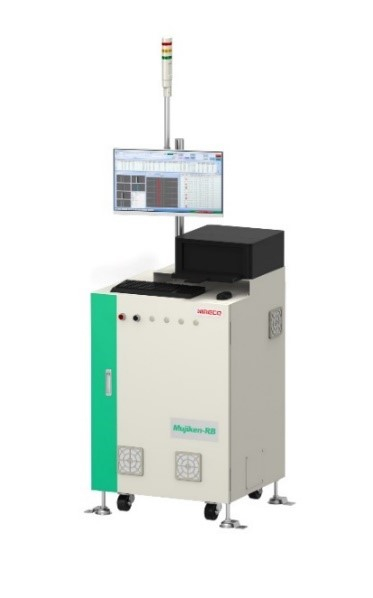
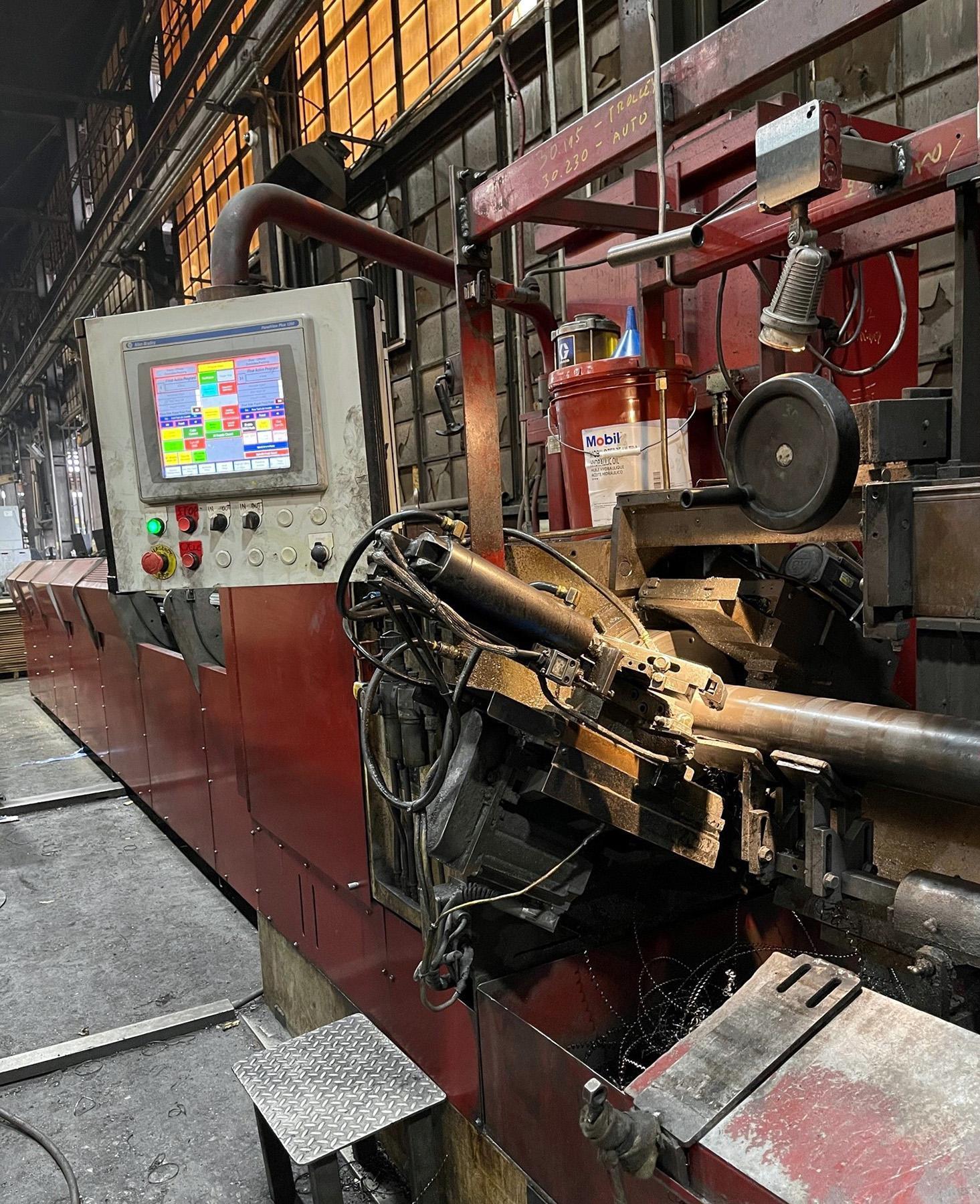
Criteria for failure in flow through conical convergine dies.
